McDonald's leverages AI technology to alleviate employee stress and improve efficiency
McDonald’s introduces cutting-edge AI technology across 43,000 locations to reduce employee stress, improve operational efficiency, and predict equipment malfunctions, including the notorious ice cream machine failures.
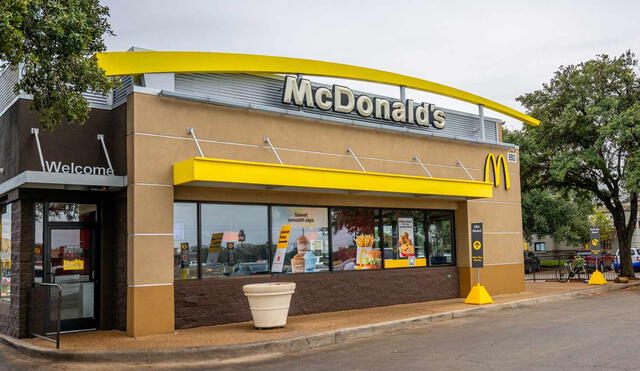
McDonald’s has begun rolling out ground-breaking AI technology across its 43,000 global locations. This strategic move aims to tackle one of the most significant issues faced by fast-food employees: stress. With a focus on enhancing the overall workplace environment, McDonald’s intends to reduce employee pressure and streamline operational processes. The new AI tools will also play a role in predicting equipment malfunctions, including the often-reported ice cream machine failures that have plagued the brand.
By incorporating artificial intelligence into their daily operations, McDonald’s is not just innovating how they serve customers, but also improving the quality of life for their staff. This technology promises to offer more than just predictive maintenance – it’s about creating a smoother, more manageable work experience for everyone involved. AI will help restaurant staff by predicting potential breakdowns in the kitchen equipment, allowing employees to focus on their tasks without the added anxiety of unexpected operational disruptions.

McDonald's AI Revolution. From Fast-Food Pioneer to Digital. Photo: Medium Composition / AI Stock Buzz.
AI-powered predictions to prevent equipment failures
A significant part of McDonald’s new AI system involves predictive technology designed to prevent unexpected breakdowns in kitchen equipment, particularly the much-maligned ice cream machines. These machines have long been a source of frustration for both staff and customers, with frequent malfunctions leading to complaints and delays. By implementing AI-driven predictions, McDonald’s aims to proactively address these issues before they disrupt operations. This shift allows restaurant managers and workers to have real-time data on the status of equipment, reducing stress and minimizing downtime.
This predictive approach isn’t limited to just the ice cream machine, however. The technology extends to other critical appliances used throughout McDonald’s kitchens. For instance, the AI system can forecast when a fryer may malfunction, ensuring that staff can perform maintenance or replacements without halting production. This leads to a more seamless workflow and, importantly, less stress on the shoulders of employees.
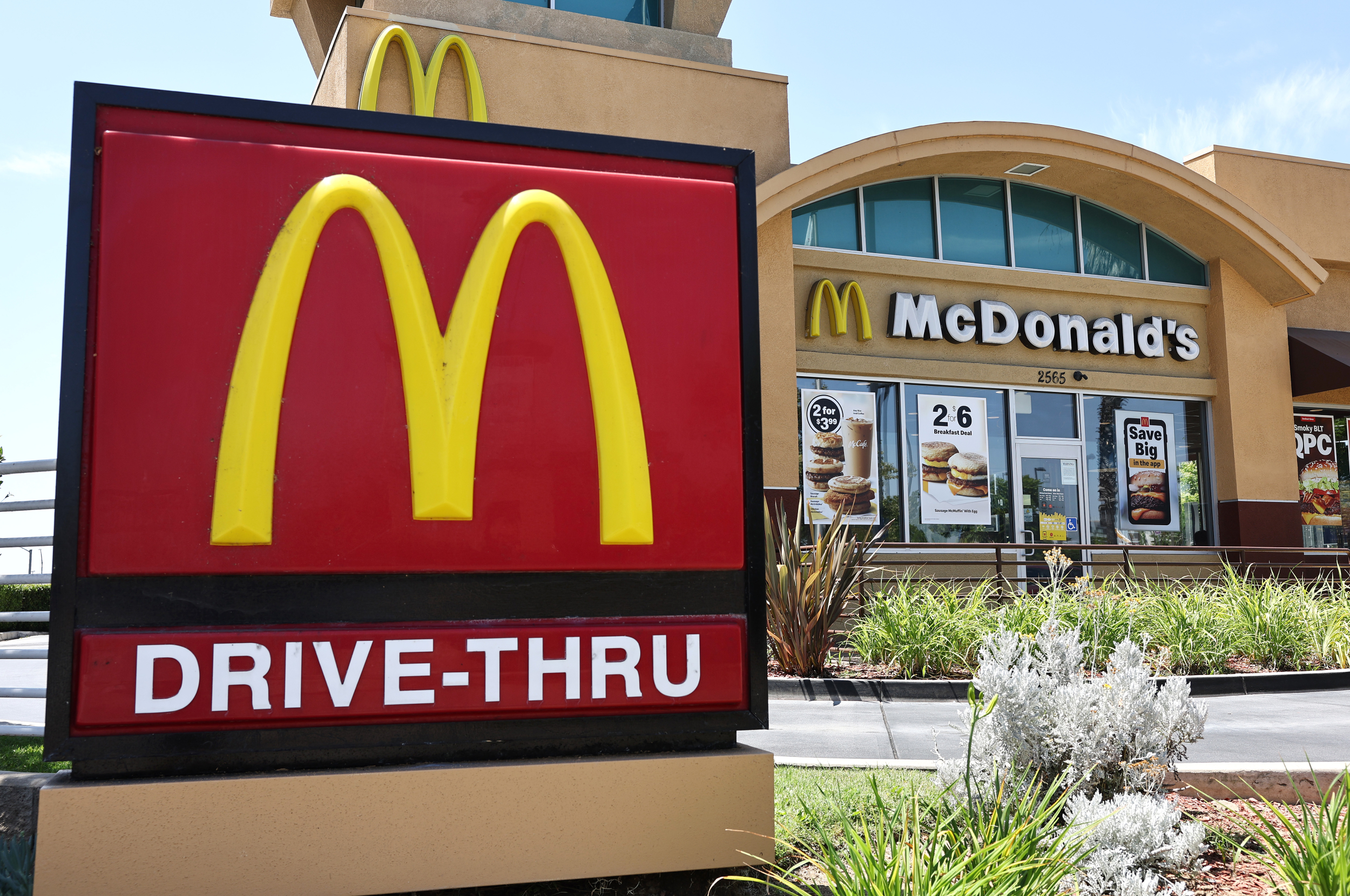
McDonald's Turns to AI to 'Alleviate Stress' of Drive-Thrus, Curbside and Increase Speed. Photo: Latin Times.
Edge computing for real-time solutions
In addition to predictive maintenance, McDonald’s has incorporated edge computing into its AI system. As mentioned, edge computing enables real-time data processing at the site of operation, allowing managers to receive instant updates about their restaurant's performance. This can include everything from kitchen operations to customer service metrics. The benefit of this system is that it provides employees and managers with immediate insights, helping them react faster to any challenges that arise during a shift.
By leveraging real-time data, McDonald’s can improve overall efficiency, reduce unnecessary workload and make more informed decisions on how to optimize staff performance. For employees, this means less time spent reacting to unforeseen issues and more time focusing on delivering a quality customer experience.